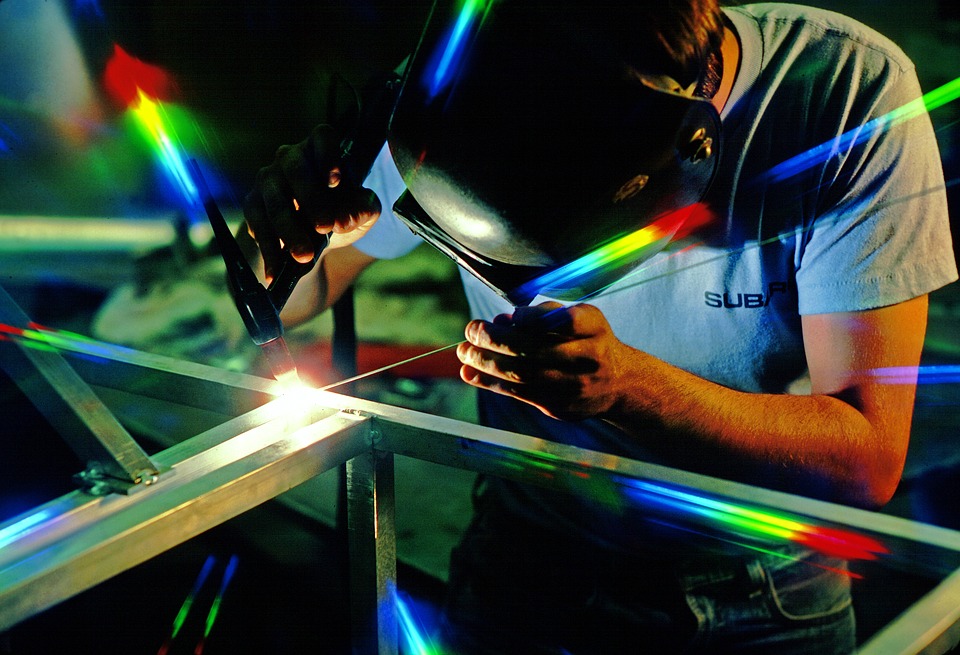
Производительность труда в России существенно уступает многим странам. У лидеров рейтинга Организации экономического сотрудничества и развития (OECD) Люксембурга и Ирландии производительность оценивается в 104,9 доллара за час, в России в 3,5 раза меньше — 29,7. И хотя по итогам последнего рейтинга 2019 года этот показатель вырос на 2,8%, сделать предстоит многое. РБК+ спросил оператора и петербургских участников национального проекта «Производительность труда» об эффективных инструментах и достигнутых результатах.
Ирина Голубцова, руководитель Регионального центра компетенций в сфере производительности труда (РЦК):
«До 2024 года в национальном проекте «Производительность труда» в Петербурге примет участие 361 предприятие. Среди задач — ежегодный 5% прирост производительности труда у 50% предприятий. Задача непростая, но выполнимая: некоторым предприятиям-участникам уже удалось превысить этот показатель, а также решить другие задачи — наладить новую производственную линию, снизить нехватку персонала. Одно из преимуществ проекта — наличие различных инструментов поддержки от аудита процессов и обучения персонала принципам бережливого производства до составления плана-графика мероприятий и создания эталонного участка. Один из новых инструментов — «Фабрика процессов». Здесь участники в реальном производственном процессе получают навыки бережливого производства и создают кросс-функциональную рабочую группу.
Для многих это проблема, так как различные подразделения просто не знают «боли» друг друга. Например, отдел продаж, подбирая новые заказы, может не учитывать возможности производства, а те, в свою очередь, не знают проблем инженеров. Еще одна задача, которую решает «Фабрика», — минимизация сопротивления. На многих производствах сотрудники работают десятилетиями, поэтому руководствуются принципом «всегда так делал». На «Фабрике» они видят, как нововведения могут оптимизировать процессы, после этого трансформация идет легче, а участники группы становятся лидерами изменений.
«Фабрика процессов» может быть полезна и тем, кто еще думает о вступлении в нацпроект: на практике можно видеть, как работают принципы бережливого производства и каких результатов можно добиться. После такого эксперимента в проект вступили уже три компании. В дальнейшем мы хотим запустить в дополнение к производственным офисные процессы и привлечь вузы, что в перспективе будет полезно для предприятий города».
Александр Шестаков, генеральный директор компании «Первая мебельная фабрика»:
«В рамках участия в нацпроекте были сформированы показатели эффективности, которых мы должны достичь в ближайшие три года: увеличить производительность на 31%, а выручку на треть — для этого есть база и все предпосылки. Мы уже освоили новые инструменты и начали стандартизировать проблемы на участках производства, оптимизировать бизнес-процессы. Это увеличило эффективность рабочего времени сотрудников до 50% без существенного увеличения ФОТ. Только на образовательных программах мы сэкономили порядка 10–15 млн руб.
В числе наиболее эффективных инструментов нацпроекта — внедрение 5С — японской системы организации рабочих мест, включающей сортировку, соблюдение порядка, содержание в чистоте, стандартизацию и совершенствование. Мы сократили время поиска необходимой фурнитуры на 25%, объем ее хранения на линии — на 40%. Выравнивание потоков позволило сократить длину перемещения продукции с 990 до 560 м, а применение стандартизированной работы увеличило выработку на линии на 30% и на 25% на одного сотрудника.
Полезной оказалась и «Фабрика процессов». В игровой форме сотрудники объединяются в команды, изучают проблемные зоны, предлагают и реализуют решения за очень короткое время, 4–5 часов. В современном мире нет конкуренции между отдельными специалистами — конкурируют команды. Победителями в этой гонке становятся наиболее эффективные и четко организованные. «Фабрика процессов» как раз является тем инструментом, который может научить коллектив работать производительнее».
Наталья Иванова, руководитель дирекции по сопровождению проектов ООО «ПСК»:
«Реалии рынка таковы, что строительная отрасль не может рассчитывать на наращивание доходности за счет увеличения конечной стоимости продукта. Поэтому все скрытые резервы для получения прибылей и оптимизации нужно искать внутри себя. Именно с этой целью мы вступали в нацпроект.
В ПСК ранее пытались собственными силами повлиять на производительность: использовали технологические карты, алгоритмирование процессов, были попытки автоматизации бумажных процессов. Но эффективно это, только если есть клуб единомышленников, вовлеченный в системный процесс, работать над которым придется всегда. Всегда — это самое сложное.
В решении этой задачи нам помогла «Фабрика процессов». Это наглядное пособие по осознанию сотрудниками масштаба проблем и их роли в процессах предприятия. На данный момент говорить о результатах рано, но уже понятно, что мы двигаемся в верном направлении».
Ольга Соловьева, начальник отдела развития производственной системы НПО Завод «Волна»:
«Входя в проект, мы ставили амбициозные цели: повышение производительности труда за счет сокращения времени изготовления изделий как в сборочном производстве, так и на участках механообработки, сокращения незавершенного производства и роста эффективности использования оборудования.
Для повышения производительности труда применяются различные элементы бережливого производства: 5С, всеобщее обслуживание оборудования, стандартизированная работа, анализ эффективности работы оборудования и др. Также проводится обучение и действует система наставничества. На данный момент нам удалось на 50% сократить время сборки изделия, повысить эффективность использования оборудования, в итоге выпуск по механозаготовительному производству вырос на 40%.
На пилотном этапе реализации проекта через «Фабрику процессов» прошли 4 человека, за 2021 год еще 22 человека. Это позволило нам повысить вовлеченность персонала в проект и получить знания и навыки, необходимые для повышения производительности труда».