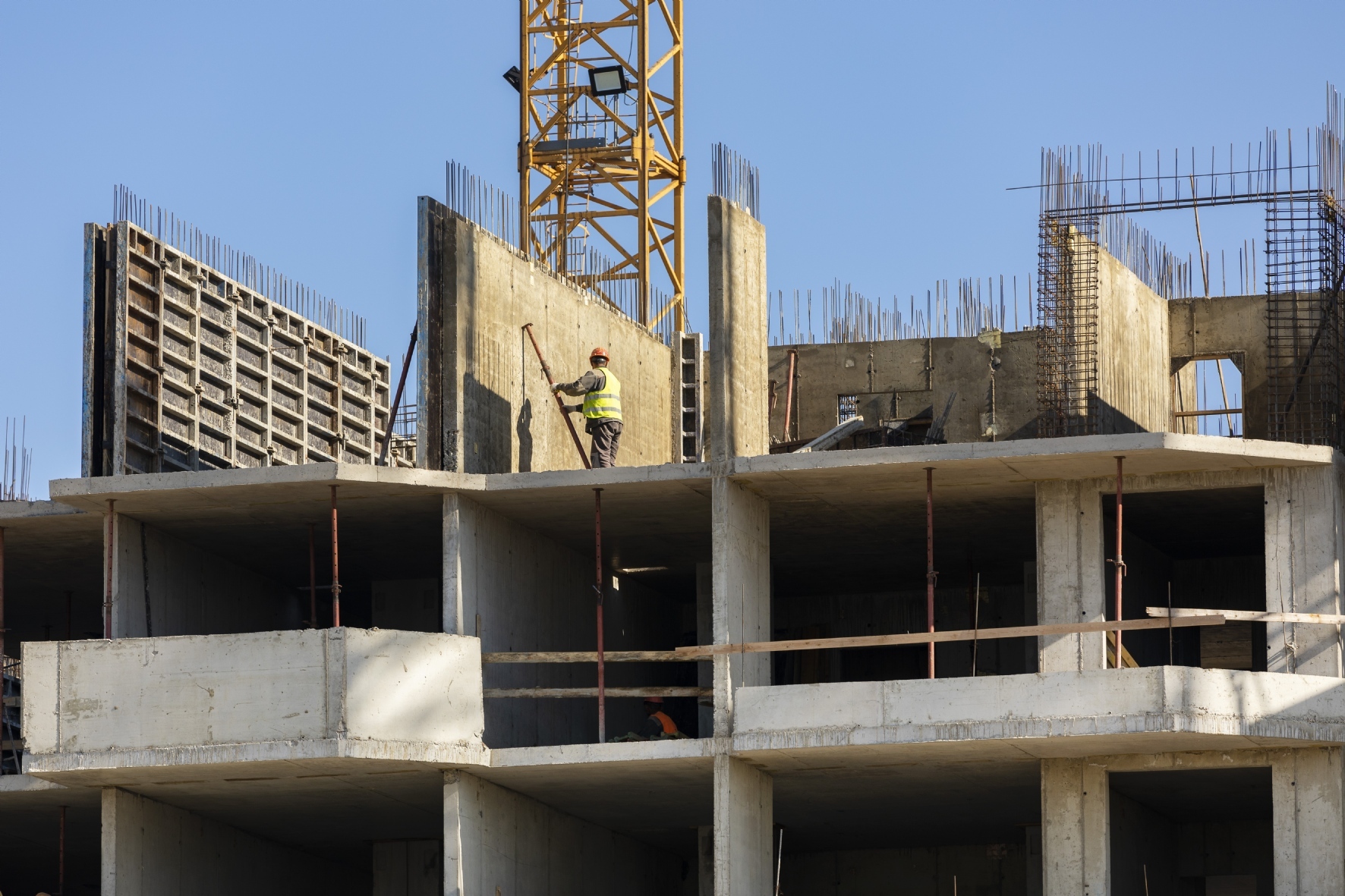
После ввода первых пакетов западных санкций весной 2022 года строительная отрасль столкнулась с необходимостью в кратчайшие сроки найти способы бесперебойного обеспечения стройматериалами. На тот момент зависимость от импортных поставок оценивалась от 10% в новостройках массового сегмента до 30% — в проектах комфорт-класса и более 50% — в элитном сегменте.
Меры господдержки, развернутые уже во втором квартале прошлого года, направленные как на стимулирование спроса, так и на прямую компенсацию части затрат на расширение и переоснащение производств стройматериалов, ускорили адаптацию рынка. Сегодня Каталог аналогов строительной продукции, созданный Национальным объединением строителей (НОСТРОЙ) совместно с Минстроем России, включает более 3000 номенклатурных позиций по всем сегментам промышленности строительных материалов и оборудования. Но ландшафт меняющегося рынка неравномерен: если в одних сегментах замещение импортных материалов отечественными практически завершилось, то в других идет сложный поиск решений.
Петербургская промышленность испытывает острый кадровый дефицит
По данным Минстроя России, в сегменте массового жилищного строительства доля импорта составляет сейчас порядка 6%. «В сегментах бизнес-класса и элитной недвижимости процент импорта достигал порядка 50% из-за использования высококачественного лифтового оборудования, инженерных систем и отделочных материалов премиального качества. Сейчас уже можно наблюдать замену европейских производителей на азиатские компании. Отечественные компании также стремятся занять «освободившиеся» ниши, именно за счет них в конкретных реализуемых проектах можно увидеть снижение доли импортных строительных материалов до 20%», — сообщил РБК Санкт-Петербург президент НОСТРОЙ Антон Глушков.
Год назад уход с рынка сразу четырех основных западных производителей лифтового оборудования сильно встревожил девелоперов: почти треть скоростных лифтов для высокоэтажных построек либо поставлялись из Европы, либо производились на заводе американской компании Otis в Санкт-Петербурге. Однако прогнозируемой катастрофы не случилось. Уже в июле 2022 года многопрофильный холдинг S8 Capital приобрел все активы американской Otis Elevator Company в России, и с августа объем производства превысил 400 единиц в месяц. Сейчас мощности отечественных заводов позволяют полностью обеспечить потребность российского рынка в лифтах для высотных домов до 40 этажей со скоростью движения до 2,5 м/с, считают в НОСТРОЙ.
Локализация производства при этом углубляется. По данным Российского лифтового объединения, год назад доля импортных комплектующих в российских производствах лифтов составляла около 30%. В основном это были лебедки для подъема кабин, закупаемые в Италии, а также в Корее, Китае и Турции. В конце 2022 года в ОЭЗ «Технополис Москва» было запущено производство лифтовых лебедок с ежегодной производственной мощностью до 1 тыс. единиц техники. В «Метеор лифт» (бывший «Отис лифт») создан собственный научно-исследовательский центр для разработки новых технологий и цифровизации производства.
Однако на то, чтобы достичь стандартов качества, соответствующих продукции ушедших западных производителей, потребуется время. Пока компании, строящие элитное жилье и высотные объекты коммерческой недвижимости, переключились на лифты из Китая.
Оголенные ниши и «незаживающая рана»
Но не все шоковые для отрасли события закончились хеппи-эндом. «Рынок инженерных систем зданий — это не просто болевая точка, это незаживающая рана в процессе импортозамещения. Нет ни одной инженерной системы, в поставки которой не пришлось бы вносить изменения, это касается и дешевых, и дорогих, и даже тех, у которых есть российские аналоги. Любой проект сегодня превращается в пазл, который в каждом случае приходится складывать по-разному, зачастую меняя не западное на отечественное, а российское на российское», — говорит генеральный директор компании «Конфидент» Петр Кузнецов.
Нет ни одной инженерной системы, в поставки которой не пришлось бы вносить изменения, это касается и дешевых, и дорогих, и даже тех, у которых есть российские аналоги.
До санкций около 70% слаботочных систем, автоматизированных систем управления, пожарной сигнализации, используемых российскими строителями, поставлялись западными вендорами. Сегодня на рынке остались только российские вендоры, которые наращивают объемы производства в 2–4 раза, но не успевают за потребностями рынка, практически не снизившимися с уровня 2018–2019 годов. В результате на продукцию «Болида», «Рубежа» и других российских вендоров образуются гигантские многомесячные очереди, и новые заказы размещаются со сроком выполнения от 3 месяцев.
Хотя пул производителей отечественных вентиляционных систем довольно велик, но их продукция во многих случаях «не проходит» по требованиям к качеству. По словам Петра Кузнецова, заказчик довольно консервативен и снижать свои требования не хочет, даже если систем «досанкционного» качества на рынке вообще нет. «Мы пользуемся всевозможными путями доставки, пытаясь привезти в РФ западную продукцию, например современные системы кондиционирования, аналогов которых в стране нет. Но ни цены, ни сроки угадать в этом случае не получается. Даже у очень крупных заказчиков, которые берут доставку на себя, используя свои каналы, видим задержку поставок на 4, 6 и даже 10 месяцев», — рассказывает руководитель «Конфидента».
Российские производители инженерных систем делятся на две категории — большинство старается поспеть за опережающим ростом спроса и наращивают объемы, меньшинство думает об усложнении производства с тем, чтобы занять высвободившиеся ниши. «Процесс требует инвестиций и времени и может состояться только при условии появления крупных высокотехнологичных проектов, формирующих запрос на сложное оборудование, а также при соответствующей поддержке государства. Иначе в перспективе 5–7 лет мы будем наблюдать тренд на упрощение строящихся объектов», — считает Петр Кузнецов.
Другую оголенную санкциями нишу обозначил заместитель генерального директора по строительным материалам «Группы ЛСР» Василий Кострица: «Большие проблемы возникли по инженерной сантехнике, начиная со смесителей, медных труб и заканчивая индивидуальными тепловыми пунктами, которыми оборудуются все дома вне зависимости от сегмента. Как оказалось, такой продукции нужного качества и нужного количества в России нет». Ранее поставки шли в основном из Европы, но из-за ослабления рубля и ненадежности логистических цепочек девелоперы переориентировались на производителей из Азии и Турции, продукцию которых стали завозить в больших объемах и использовать в более высоких ценовых сегментах жилья. «Новые условия требуют новых подходов в логистике: теперь, чтобы не допускать перерывов в строительстве, приходится заказывать поставки за 3–4 месяца», — говорит Василий Кострица.
Базовые: «можно обойти историю с санкциями»
В мае-июне 2022 года Аналитический центр промышленности строительных материалов CM PRO, изучив рынок, пришел к выводу: внутреннее производство базовых строительных материалов способно полностью обеспечить потребности строительной индустрии. В поставках на рынок кабельной продукции, керамического кирпича, цемента, линолеума, полимерных труб доля импорта была ничтожно мала; в поставках стекла, дверей, газобетона, лакокрасочных материалов, минеральной изоляции не превышала 8%. Однако при этом отмечалась критическая зависимость стратегически важных для отрасли производств от западного оборудования и запчастей: их доля оценивалась от 70% (цемент) до 100% (ламинат, паркетная доска, кабельная продукция, полимерные трубы). Совершенно независимыми от подсанкционного оборудования оказались только кирпич ручной формовки и лакокрасочные строительные материалы.
Российское производство базовых стройматериалов способно полностью закрыть потребности внутреннего рынка. Но оно критически зависит от импортного оборудования.
К весне 2023 года, по данным CM PRO, ситуация не изменилась (см. график) — выпуск отечественного оборудования за год наладить просто невозможно. Но бизнес приспосабливается к обстоятельствам. Как рассказал Василий Кострица, в производстве строительных материалов «Группы ЛСР» программа импортозамещения была запущена несколько лет назад. Из соображений экономии импортные детали более простых линий (например, камнедробилок) постепенно заменяли отечественными аналогами. Прошлогодние санкции добавили процессу скорость и масштаб: очень быстро пришлось искать российских производителей комплектующих также для высокотехнологичного оборудования, а там, где это невозможно, — наладить альтернативные каналы поставок. «В поиске новых поставщиков сильно помогает глобализация рынка. Если взять завод по производству, скажем, гранитного щебня от любого известного западного поставщика, то он состоит из узлов и компонентов, закупленных в той же Азии. Поэтому, зная каталожный номер детали, находим ее производителя и заказываем непосредственно у него. Это сложнее и дольше, чем раньше, но можно спокойно обойти историю с санкциями», — поясняет Василий Кострица. По его словам, прямой выход на производителя позволяет компенсировать возросшие транспортные расходы отсутствием наценки к стоимости за европейский бренд.
Схожим образом справились с вызовами переработчики камня из Карелии. «В нашем технопарке установлено оборудование из Китая и Италии. С Китаем проблем нет. Большая часть итальянских комплектующих заменяется на российские аналоги. В случае отсутствия российских аналогов выходим на азиатский рынок. Горюче-смазочные материалы, используемые для обслуживания, коагулянт для очистки воды полностью замещены продукцией отечественного производства», — рассказал председатель Ассоциации камнеобрабатывающих предприятий в Карелии Дмитрий Фабрикантов. По его словам, импортозамещение оборудования не отразилось на результатах деятельности: по итогам производственной деятельности в 2022 году общий оборот резидентов технопарка «Южная промзона» вырос в 2 раза, а география рынков сбыта расширилась.
В начале пути
«Работа над Каталогом наглядно продемонстрировала, что не найти отечественный или производства дружественных государств аналог импортного материала практически невозможно», — говорит Антон Глушков. Помимо лифтов, собеседник перечислил другие сегменты, в которых замещение прошло без затруднений. За год с небольшим удалось заменить на отечественную практически всю запорную и регулирующую арматуру, кабельную продукцию, трубы, фитинги, часть строительной химии. Осенью 2022 года на мощностях Курганского завода комплексных технологий заработала линия по производству полиэтиленовой трубы ПЭ100 от 32 до 160 мм, в том числе из вторичного сырья, с годовой производительностью 250 погонных километров. Успешно реализован проект по производству синтетических смол для композитной отрасли в Ярославле.
Однако говорить о завершении процесса пока не приходится. По данным НОСТРОЙ, отечественные предприятия могут самостоятельно выпускать только 30% необходимого объема минеральной изоляции, 20% сухих смесей и 10% строительной химии. Лакокрасочная продукция и монтажная пена по-прежнему на 75% состоят из зарубежного сырья. Значительная часть фасадной плитки, саморезов, герметиков, клея импортируется. Рынок керамогранита также зависит от иностранного сырья, оборудования и запчастей. Необходимо расширить производство преднапряженной арматуры и вант, оборудования для систем вентиляции и кондиционирования, обеспечения пожарной безопасности, фасадной клинкерной плитки, качественного крепежа.
«Безусловный плюс — это развитие отечественной промышленности строительных материалов, создание новых и расширение действующих производств, дополнительных рабочих мест, увеличение объемов производства инновационной строительной продукции, благоприятные условия для отечественных производителей и вхождения их продукции на рынок. Из минусов могу назвать разорванные привычные партнерские связи и логистические цепочки», — подводит промежуточный итог Антон Глушков.
«Покупаешь новый импортный завод — и через несколько лет он становится наполовину отечественным»
Производство базовых строительных материалов, по оценке Аналитического центра промышленности строительных материалов, критически, на 70–100%, зависит от импортного оборудования. О том, как справляются с этой зависимостью крупные производители, рассказал заместитель генерального директора по строительным материалам «Группы ЛСР» Василий Кострица.
— Как сказались санкции на производстве строительных материалов в группе?
— Традиционно производители базовых строительных материалов минимально зависят от импортного сырья. Импортные добавки в производстве бетона или газобетона практически не применялись: химическая промышленность в РФ всегда была неплохо развита, и большая часть компонентов давно производится в России из российского же сырья. Пожалуй, один из немногих компонентов, который мы пока не можем «импортозаместить», — это марганец тетраоксид, необходимый для производства кирпича. Его просто нет в России нужного стабильного качества. Устраивающий нас по качеству есть в ЮАР. Южно-Африканская Республика к санкциям не присоединилась, и мы продолжаем ввозить сырье по отработанной схеме.
— Базовые стройматериалы производятся на западном оборудовании. Как решали вопросы с поставкой комплектующих?
— Санкции создали нам сложности с нашими технологическими линиями, но никоим образом не поставили под вопрос работу производств. Мы и раньше занимались импортозамещением оборудования там, где это возможно, — из соображений экономии. Такая программа была запущена в ЛСР несколько лет назад, а история с санкциями просто подстегнула эту работу, с прошлого года она стала более масштабной. Любое оборудование делится на высокотехнологичное и вспомогательное. Зачем покупать комплектующие для вспомогательного, сравнительно несложного оборудования в Европе или даже в Азии, когда их спокойно можно сделать в России? Покупаешь новый импортный завод, к примеру, по производству щебня, и через несколько лет в процессе эксплуатации он становится уже комбинированным — наполовину, а то и более, отечественным.
С прошлого года стали и в высокотехнологичном оборудовании также по возможности замещать узлы и элементы на российские. Там, где это невозможно, нашли новые каналы поставок. Везем из Азии, стараясь выйти напрямую на производителя. Это, конечно, требует иного подхода к планированию заказов, теперь комплектующие могут идти к нам несколько месяцев. Но на цене оборудования новая логистика сказывается несильно, так как более длительный путь поставок компенсируется отсутствием наценки европейских, американских и прочих «брендовых» поставщиков.
— Почему тогда выросли цены на бетон? По данным портала mcena.ru, с начала года он в среднем подорожал на 7%. У вас тоже?
— У нас тоже отпускная цена выросла, но несколько меньше — на 6%. И произошло это точно не за счет новой логистики. Причины — в инфляционном росте затрат на производство. Энергоресурсы повысились в цене, сырье за это время сильно подорожало: цемент — на 26%, песок — на 14%, щебень — на 25%. На этом фоне 6-процентное повышение цены на бетон выглядит более чем скромно. К тому же сильно меняется рынок труда. Уже ощутим дефицит квалифицированных рабочих кадров, и, соответственно, затраты на их привлечение тоже будут расти.
Третья причина — маркетинговая: в прошлом году ЛСР принял решение о сокращении производства бетона за счет ухода из массового сегмента строительства в более высокомаржинальный.
— Поэтому вы недавно выставили на продажу один из бетонных заводов в Санкт-Петербурге?
— Мы не собираемся сворачивать производство бетона, наоборот, сейчас в соответствии с ситуацией на рынке недвижимости принято решение о возвращении в массовый сегмент. Из-за особенностей спроса будем опять зарабатывать на больших объемах.
Что касается сообщений в СМИ о продаже завода, информация не вполне верна. ЛСР продает участок на Софийской улице, а не бетонное производство. Изначально здесь производилась перевалка песка и щебня с железнодорожного транспорта на автотранспорт. Сейчас вся перевозка осуществляется автотранспортом, и площадка должным образом не загружена. Было принято решение выставить участок на продажу, а полученные средства инвестировать в развитие.
В отношении завода рассматриваем разные варианты: перенести на другую площадку, законсервировать, арендовать пятно у нового владельца земли или, если будет интерес, продать вместе с участком. Но ни один из вариантов не приведет к сокращению производства бетона: сейчас у ЛСР четыре действующих завода и один законсервированный, который мы при необходимости легко вернем в строй.
— Производство песка, газобетона, судя по отчету ЛСР, за первый квартал 2023 года, тоже просело на 30–40% по сравнению с прошлым годом. С чем это связано?
— Исключительно с динамикой рынка. Ситуация сейчас непростая. Крупные инфраструктурные дорожные проекты в нашем регионе поставлены на паузу или развиваются в вялотекущем режиме, дороги не строят — спроса на песок нет. С началом СВО, по крайней мере в Санкт-Петербурге, Ленинградской области, загородный рынок встал, строительство не ведется. Соответственно, спрос на газобетон упал.
— Как реагируете на сокращение спроса?
— Осваиваем новые рынки. Поэтому, например, у нас подросло производства гранитного щебня. Начали его отгрузку морем в Калининград. Там совсем нет своего гранита, и щебень всегда был завозной. Везли из Польши, из Беларуси и даже из Швеции морем. Сейчас по понятным причинам из традиционных поставщиков остались только белорусы, и мы пришли. Более активно осваиваем другие регионы — Ярославль, Нижний Новгород, сильно увеличили отгрузку в Москву. Доля поставок кирпича в регионы также сильно выросла — везем в Нижний Новгород, Рязань, Самару, Казань, даже в Казахстан отгрузки были. Адаптируемся к новым условиям.