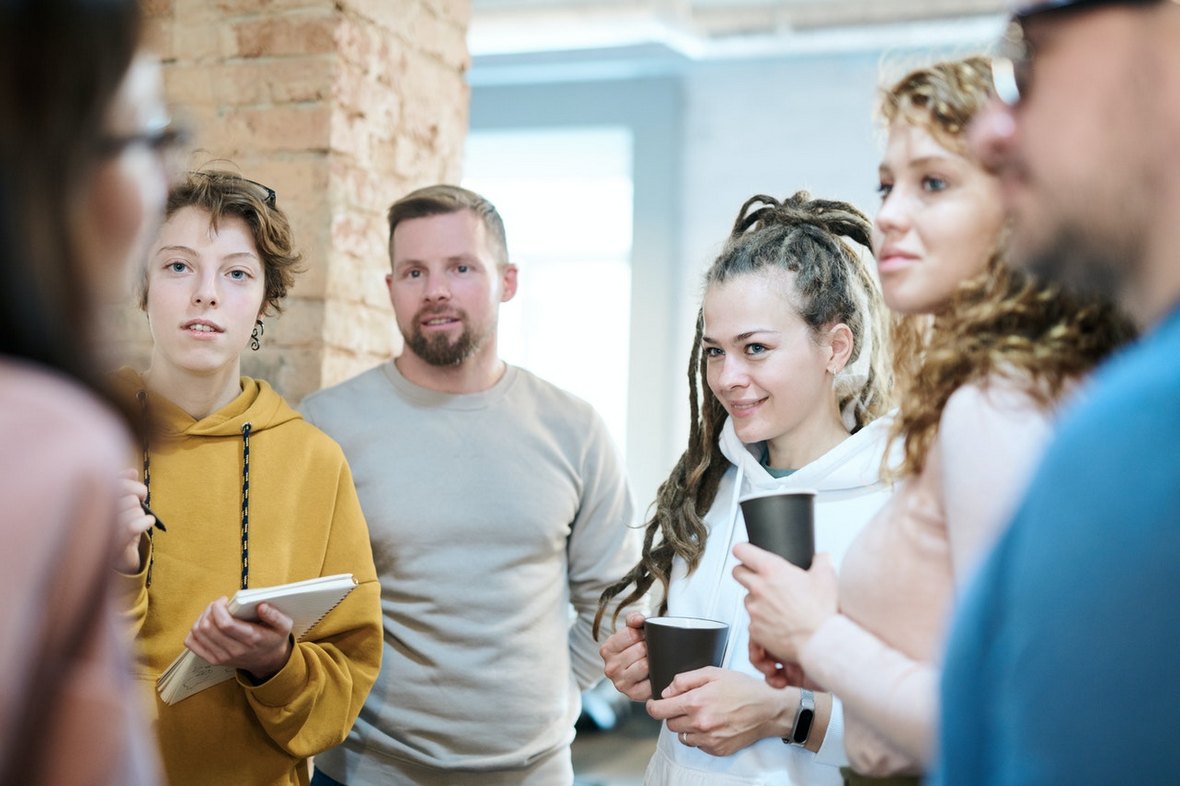
В условиях коронакризиса, нарастающей конкуренции и кадрового голода во всех индустриях предприятия все больше внимания уделяют вопросам повышения производительности труда. Один из косвенных индикаторов — включение в национальный проект «Производительность труда». По России уже 3 тыс. предприятий вошли в программу, в Петербурге — 100. При этом как в рамках проекта, так и при самостоятельном внедрении новых методик и инструментов, компании сталкиваются с одной и той же проблемой: сопротивлением со стороны сотрудников. Однако участники организованной РБК Петербург дискуссии «Внутренние резервы: как повысить эффективность бизнеса» уверены, преодолеть его возможно.
Преодолевая сопротивление
Повышение производительности труда требует чаще всего радикальных изменений, которые затрагивают линейный персонал: им приходится включаться в изменения, обучаться, перенимать непривычные им практики. Людям перемены редко нравятся, и, как отметили участники дискуссии, убедить сотрудников, рассказывая им о необходимости повышать производительность для блага предприятия, редко получается.
«Люди к подобным инициативам зачастую относятся скептически, думая, что руководство заставляет заниматься ненужным», — отмечает исполнительный директор «ГринСалат» Андрей Пайгусов.
И даже статистика прироста выпуска продукции в компаниях, которые уже внедрили бережливое производство или другие инструменты, не всегда убедительна — для преодоления сопротивления со стороны линейного персонала приходится искать другие инструменты убеждения и мотивации. Например, за счет привлечения внешних кураторов и специалистов. «Мы озабочены вопросами повышения производительности, стараемся мониторить все процессы жизненного цикла, — говорит руководитель службы бизнес-процессов и качества АРМАН Холдинг Владлена Борисова. — Наш холдинг — самоорганизующаяся система, поэтому мы для решения подобных задач привлекаем внешних спикеров, в том числе использующих интерактив как инструмент повышения заинтересованности аудитории».
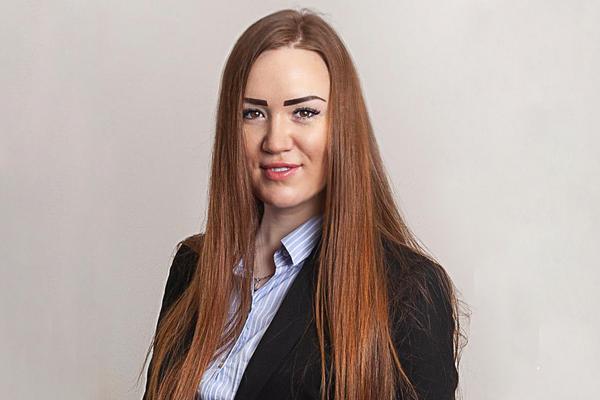
Среди применяемых холдингом инструментов — бережливое производство, теория ограничений [методология управления системами в различных видах деятельности, основанная на поиске и управлении ключевым ограничением системы, которое предопределяет успех и эффективность всей системы в целом – ред.]. Это, по мнению Владлены Борисовой, позволяет улучшить процессы. Вовлекать же в трансформацию сотрудников позволяет заинтересованность топ-менеджмента и система мотивации — как материальной, так и нематериальной — в том числе признание заслуг руководством и коллективом.
Фабричный подход
В рамках нацпроекта «Производительность труда» кроме стандартных инструментов — инфоцентра, системы наставничества и т.д., запустили «Фабрику процессов». Это деловая игра, участники которой в реальном производственном процессе получают практический опыт применения инструментов бережливого производства. В течение одного дня за три игровые смены тренеры воссоздают ситуации, возникающие на предприятии, и показывают на практике, как можно повысить эффективность труда.
Применение игрового сценария позволяет иначе взглянуть на производственные процессы. «Участие в «Фабрике» во многом позволило изменить отношение персонала к проекту по повышению производительности труда. К тому же программа «Фабрики» рассчитана так, чтобы люди не уставали, а вовлекались в процессы — игровая механика оказалась очень кстати», — говорит Андрей Пайгусов.
Как пояснила директор по аналитике и коммуникациям Регионального центра компетенций в сфере производительности труда Санкт-Петербурга (РЦК) Наталья Левкина, на «Фабрике» командой участников создается реальное изделие — регулятор давления газа, состоящий из 28 комплектующих. Все процессы производственного предприятия полностью воспроизведены на площадке, и в рамках игры с помощью инструментов бережливого производства команда сама генерирует варианты оптимизации производства, снижения себестоимости, минимизации потерь, влияющих на экономическую модель предприятия. При этом участники видят проблемы и проводят параллели с тем, как все устроено на их предприятии.
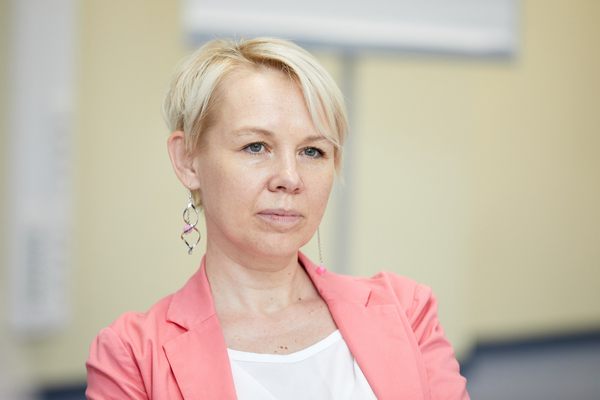
По словам менеджера по персоналу компании «СпортЭго» Карины Верещагиной, несовпадение отраслевой специфики производства на «Фабрике» и в компаниях, которые представляет команда, не мешает обучению и вовлечению. «Наши сотрудники уже дважды участвовали в «Фабрике процессов». И хотя производились незнакомые нам изделия, мы сделали выводы о том, насколько важна правильная расстановка рабочих мест, грамотное выявление ошибок на участке ОТК с целью передачи на переделку именно на ту операцию, где был допущен брак. Смена ролей также оказалась полезна: это позволяет взглянуть на задачи с другой стороны. Мы трижды изготавливали деталь, и было интересно наблюдать, как меняется время изготовления детали при трансформации ряда процессов. Полученные знания мы потом применили на своем производстве, пересмотрев многие процессы», — рассказала Карина Верещагина.
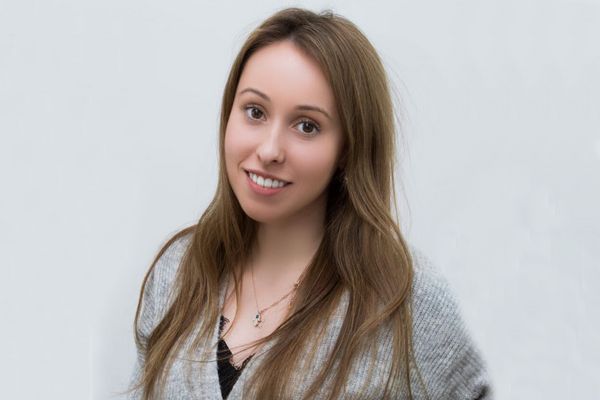
Примечательно, что «Фабрика процессов» демонстрирует приверженность культуре непрерывных улучшений, в которую старается вовлечь и участников. «Так как мы тоже живем в переменчивом мире, система непрерывных улучшений встроена в проект. Например, к «Фабрике производственных процессов» добавляется «Фабрика офисных процессов», созданная по запросу предприятий. Уже началось пилотирование, и в начале декабря состоится ее официальное открытие. А потом, возможно, появятся и другие фабрики — например, логистическая и другие», — прогнозирует Наталья Левкина.
Ставка на результат
Для руководящего состава предприятий, конечно, значимой мотивацией являются достижения бизнес-результатов — в том числе, тех, которые демонстрируют другие предприятия.
Иногда даже собственный опыт оказывается стимулом. Например, в компании «ЭлектронМаш» на предприятии, специализирующемся на выпуске электротехнического оборудования, уже более 10 лет внедрены принципы бережливого производства, и казалось, что уже нечего оптимизировать. Тем не менее, акционеры настаивали на дальнейшем повышении производительности труда для обеспечения более конкурентного положения компании на рынке. «Электронмаш» присоединился к национальному проекту в середине 2021 года, и по итогам участия запланировано увеличение производительности труда примерно на 25%.
«Совместно с экспертами ФЦК мы провели оптимизацию и реинжиниринг основных производственных процессов и выделили несколько главных направлений улучшений, - рассказывает заместитель генерального директора по качеству АО «ЭлектронМаш» Андрей Фоменков. - Это изменение процессов комплектации изделий и доставки их на конвейер, что уже обеспечило прирост производительности в 5-10% в зависимости от продукции. На следующем этапе мы провели оптимизацию расположения станочного парка, что привело к сокращению времени на перемещение и обеспечило прирост 5-10%. А оптимизация сборочного процесса и процесса испытаний на основании двух предыдущих изменений позволит нам достичь планируемого командой проекта результата в 25%».
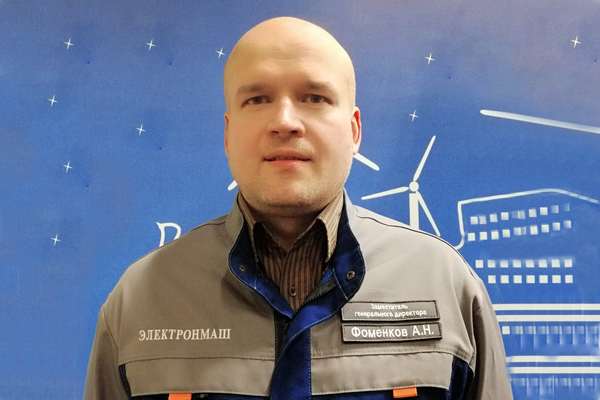
Есть и результаты, которые сложно измерить, но для топ-менеджеров они о многом говорят. В компании «ГринСалат» уже после первого этапа проекта улучшились показатели производительности труда на одного человека, снизилось время протекания процесса и запасы незавершенного производства. «Первый этап наложился на «ковид», упали объемы, появились серьезные кадровые проблемы в связи с оттоком сотрудников из числа трудовых мигрантов. Но мы увидели, что нацпроект помогает: мы почти безболезненно пережили кризис», — говорит Андрей Пайгусов.
«Петербург вступил в нацпроект лишь в 2019 году, так что показатель в 100 предприятий-участников — достойный результат. Многие руководители бизнеса не спешили присоединяться к проекту, потому что сначала хотели посмотреть, каких результатов удастся добиться. Сейчас, когда бизнес уже прочувствовал преимущества проекта, мы видим 2-3 заявки на участие в день — это позитивная динамика, внушающая оптимизм», — резюмирует Наталья Левкина.